Picking The Ideal Pressure Filter for the Market
페이지 정보

본문
Selecting the perfect pressure filter for your market may be a overwhelming task, especially with the array of choices present in the market.
From chemical treatment and chemical processing to food and beverage production, exist various sectors that demand personalized filtration solutions.
Despite, each market owns its distinct set of requirements, limits and working conditions that govern the selection of a pressure filter.
When picking a filtration equipment, the initial aspect should be the nature of the fluid for filtered. Filtration equipment can be used for both both liquid-liquid and solid-liquid separation.
Considering the physical and chemical features of the fluid, such as its particles concentration, flowability and pH level, can enable find the ideal filtration equipment design and components of assembly.
For example, a fluid with high solids content may require a filter press with reinforced frames and a higher solids discharge rate.
Yet another critical factor in picking the ideal filtration equipment is the flow rate of the fluid. Higher flow rates demand a more robust designs, as the fluid must be filtered at a frequency that meets production requirements.
That may involve larger filter chambers and improved cake washing Functions.
In contrast hand, low flow rates may enable a more compact design with more manageable filtration forces.
In addition to fluid properties and flow rates, the scale of operation as well significantly influences filter press selection. Commercial operations require more substantial filter presses, often measuring metres in size, to meet high filtration required.
With contrast, compact operations usually opt for more compact, energy-efficient models.
Maintenance costs are also crucial considerations when picking a pressure oil filter manufacturing machine. Automating specific processes such as the backwash process and cake discharge system, can significantly reduce labor demands and decrease downtime consequences.
Pressure filter design innovations, such as the use of synthetic materials and advanced coatings, can also reduce maintenance requirements and minimize the impact of corrosion on the equipment.
Compliance compliance is another essential aspect to consider. Filtration equipment must often meet specific regulatory standards for environmental conservation and worker safety. As such, the chosen filtration equipment should be designed and built with compliance in mind, incorporating a range of features that minimize waste generation and minimize the risk of equipment failure.
Working with experienced pressure filter manufacturers and engineers is recommended to ensure that the selected filtration equipment aligns with the specific needs of your industry. Considering your operation's unique requirements, you may also find it beneficial to consider customizing your pressure filter or hybridizing multiple technologies to optimize performance and efficiency.
Irrespective of the industry you belong to, picking the ideal filter press requires deliberate consideration of various factors, including the fluid properties, flow rates, scale of operation, maintenance and operating costs, and regulatory compliance. By taking a well-informed and comprehensive approach to filter press selection, you can ensure optimal filtration performance, minimized risks, and maximum return on investment for your operation.
From chemical treatment and chemical processing to food and beverage production, exist various sectors that demand personalized filtration solutions.
Despite, each market owns its distinct set of requirements, limits and working conditions that govern the selection of a pressure filter.
When picking a filtration equipment, the initial aspect should be the nature of the fluid for filtered. Filtration equipment can be used for both both liquid-liquid and solid-liquid separation.
Considering the physical and chemical features of the fluid, such as its particles concentration, flowability and pH level, can enable find the ideal filtration equipment design and components of assembly.
For example, a fluid with high solids content may require a filter press with reinforced frames and a higher solids discharge rate.
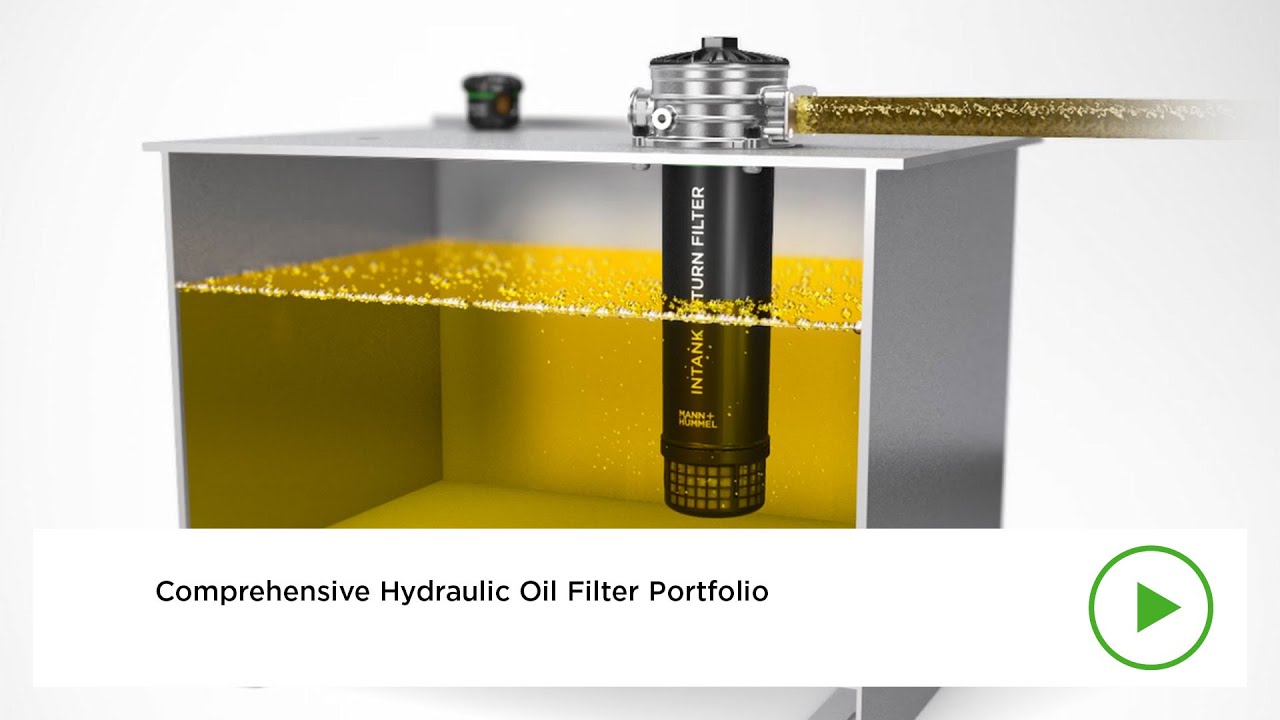
That may involve larger filter chambers and improved cake washing Functions.
In contrast hand, low flow rates may enable a more compact design with more manageable filtration forces.
In addition to fluid properties and flow rates, the scale of operation as well significantly influences filter press selection. Commercial operations require more substantial filter presses, often measuring metres in size, to meet high filtration required.
With contrast, compact operations usually opt for more compact, energy-efficient models.
Maintenance costs are also crucial considerations when picking a pressure oil filter manufacturing machine. Automating specific processes such as the backwash process and cake discharge system, can significantly reduce labor demands and decrease downtime consequences.
Pressure filter design innovations, such as the use of synthetic materials and advanced coatings, can also reduce maintenance requirements and minimize the impact of corrosion on the equipment.
Compliance compliance is another essential aspect to consider. Filtration equipment must often meet specific regulatory standards for environmental conservation and worker safety. As such, the chosen filtration equipment should be designed and built with compliance in mind, incorporating a range of features that minimize waste generation and minimize the risk of equipment failure.
Working with experienced pressure filter manufacturers and engineers is recommended to ensure that the selected filtration equipment aligns with the specific needs of your industry. Considering your operation's unique requirements, you may also find it beneficial to consider customizing your pressure filter or hybridizing multiple technologies to optimize performance and efficiency.
Irrespective of the industry you belong to, picking the ideal filter press requires deliberate consideration of various factors, including the fluid properties, flow rates, scale of operation, maintenance and operating costs, and regulatory compliance. By taking a well-informed and comprehensive approach to filter press selection, you can ensure optimal filtration performance, minimized risks, and maximum return on investment for your operation.
- 이전글Married Drivers Are Risking Their No 25.04.01
- 다음글See What Car Key Repair Tricks The Celebs Are Utilizing 25.04.01
댓글목록
등록된 댓글이 없습니다.